Context
Recently, Indian Space Research Organisation (ISRO) successfully tested a liquid rocket engine made with the help of additive manufacturing technology commonly known as 3D printing.
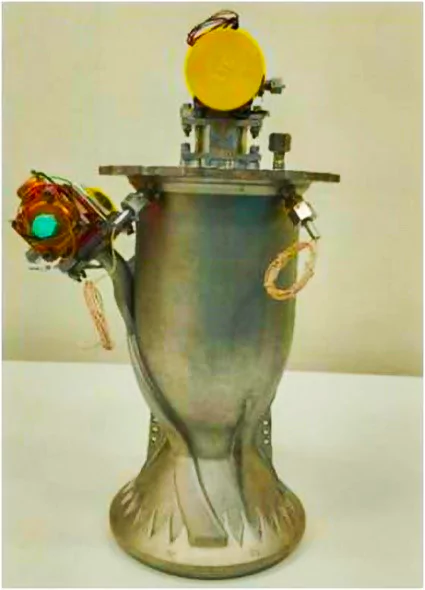
About PS4 Engine – ISRO 3D-printed Liquid Rocket Engine
- The PS4 engine, which is used as the engine for the fourth stage of the Polar Satellite Launch Vehicle (PSLV), was redesigned by ISRO for production using 3D printing.
- It was developed by ISRO’s Liquid Propulsion Systems Centre (LPSC)
- Type: Liquid Rocket Engine
- Propellant: It uses Earth-storable bipropellant combinations, nitrogen tetroxide and monomethylhydrazine as propellants in a pressure-fed system.
- Thrust: Approximately 7.3 kN .
- Function: The fourth stage is the final stage of the PSLV.
- It performs the precision orbit insertion for the satellite payload. Its liquid engine allows for precise orbital adjustments.
- The PS4 engine is also utilized in the Reaction Control System (RCS) of the initial stage (PS1) of the PSLV rocket.
The RCS controls a rocket, or spacecraft’s orientation, ensuring stability and maneuvering using small thrusters, enabling precise control for such tasks as attitude control during ascent, precise trajectory adjustments for stage separation, payload deployment and docking maneuvers.
- The engine was manufactured by M/s WIPRO 3D in India and underwent hot testing at the ISRO Propulsion Complex at Mahendragiri.
- The LPSC revamped the engine to align with the Design for Additive Manufacturing (DfAM) approach.
Enroll now for UPSC Online Course
Why did ISRO use 3D printing to build the PS4 engine?
- The technology helped ISRO bring down the number of parts in the engine from 14 to a single piece.
- To eliminate 19 weld joints and save 97% of raw material.
- It also reduced the overall production time by 60%.
What is 3D printing?
- 3D printing is a process that uses computer-created design to make three-dimensional objects layer by layer.
- It is an additive process, in which layers of a material like plastic, composites or bio-materials are built up to construct objects that range in shape, size, rigidity, and colour.
- Materials used : including thermoplastics such as acrylonitrile butadiene styrene (ABS), metals (including powders), resins and ceramics.
How is 3D printing done?
- Essentials: To carry out 3D printing, one needs a personal computer connected to a 3D printer.
- Similarity with Traditional Printers : The (3D) printer acts generally the same as a traditional inkjet printer in the direct 3D printing process.
- In it a nozzle moves back and forth while dispensing a wax or plastic-like polymer layer-by-layer, waiting for that layer to dry, then adding the next level.
- Process:
- Design a 3D model of the required object on computer-aid design (CAD) software and press ‘print’. The 3D printer does the rest of the job.
- Layering Method : 3D printers construct the desired object by using a layering method, which is the complete opposite of the subtractive manufacturing processes.
- 3D printers, on the other hand, build from the bottom up by piling on layer after layer until the object looks exactly like it was envisioned.
- It adds hundreds or thousands of 2D prints on top of one another to make a three-dimensional object.
- Common 3D print technologies include:
- FDM (fused deposition modeling): A print technology that extrudes a thermoplastic filament to create the layer-by-layer model.
- SLS (selective laser sintering): A polymer powder print technology,Pre-heated to its melting point, it is selectively melted with a CO2 laser, fusing the particles together to create a solid part.
- SLA (stereolithography): A print technology where a photosensitive liquid resin is solidified under an ultraviolet laser.
- PolyJet: A print technology that uses liquid photopolymers and builds parts by depositing the ultrafine droplets of these liquid photopolymers on a build platform through the print head(s).
- Utility:
- It has the capability of printing anything from ordinary objects like a ball or a spoon to complex moving parts like hinges and wheels.
- Or It can print a whole bike – handlebars, saddle, frame, wheels, brakes, pedals and chain – ready assembled, without using any tools.
Enroll now for UPSC Online Classes
Additive vs. subtractive manufacturing comparisons
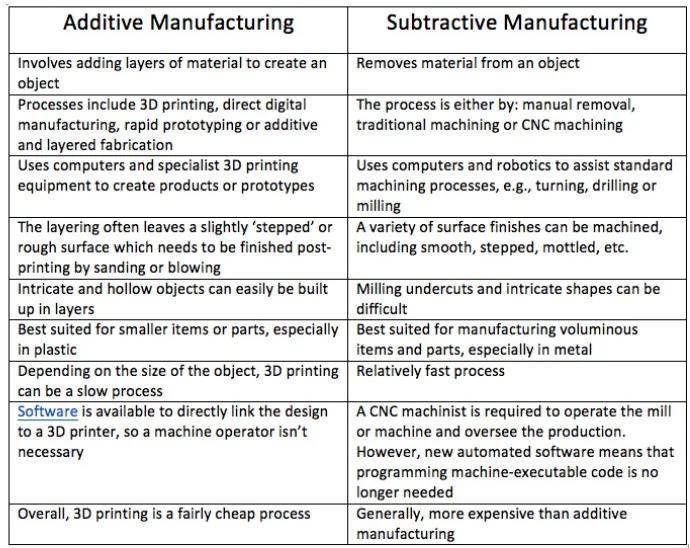
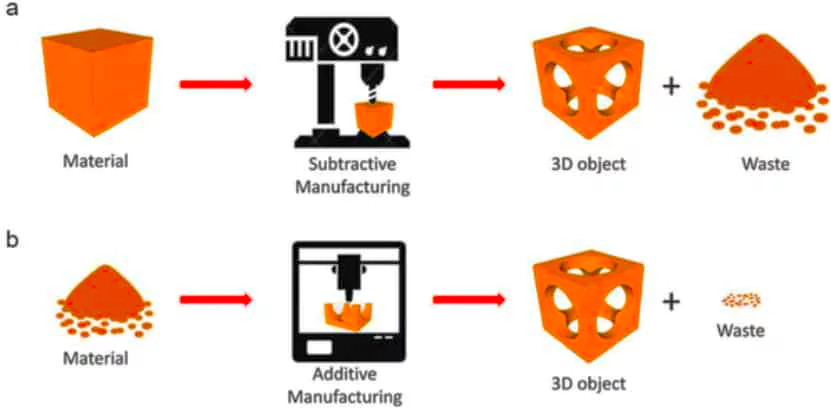
Also Read: Orbital Debris Mitigation: ISRO’s Zero Debris Milestone